
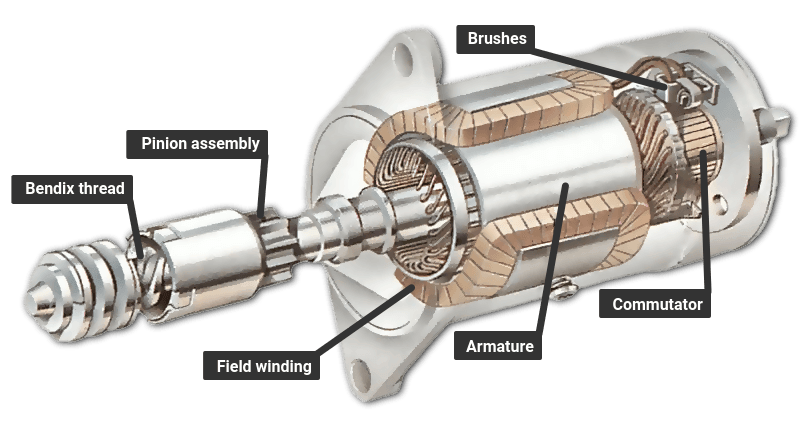
Using either AC or DC voltage, the hipot test involves applying current between electrical circuits and the frame. Performed as a detection of weakness and potential for failure within cable or wire insulation, high potential (hipot) testing, also known as dielectric strength testing, should be performed after conducting initial visual inspection and insulation resistance tests. The Hipot Test for Dielectric Strength: Determining Efficacy of Cable Insulation But by dedicating time to thorough motor testing - both in regular, routine maintenance programs and at the first sign of trouble - motor issues can be reliably predicted, prevented, isolated, and resolved with minimal service disruption.īelow are just a few of the many motor tests available. Motor failure, therefore, can be extremely costly and disruptive, resulting in unscheduled downtime and unplanned maintenance costs. Without motors, many basic industrial functions would be severely compromised, if not impossible motors are the heartbeat of daily work. Motor Test Methods: Isolating the ProblemĬomplex, powerful tools, electric motors are critical components in a wide range of equipment and tools, from the smallest electronic fans to the largest manufacturing and industrial equipment. Preliminary tests are generally done using the ubiquitous multimeter, which can provide diagnostic information for all kinds of motors. And depending on the specific area of trouble, each tool can help illuminate the problem in different ways.Ī good rule of thumb for troubleshooting a motor is to first rely on your senses: Is the motor hot or overheating? Does it smell or sound unusual? Is it physically behaving in an erratic way? To begin an evaluation, check in first on the basic measures of motor performance: current levels, power, voltage, and resistance. There’s a huge range of diagnostic tools available for pinpointing motor issues - clamp-on ammeters, temperature sensors, Meggers, winding analyzers and oscilloscopes, just to name a few. Basic Motor Testing Parameters and Tools: Primary Analysis

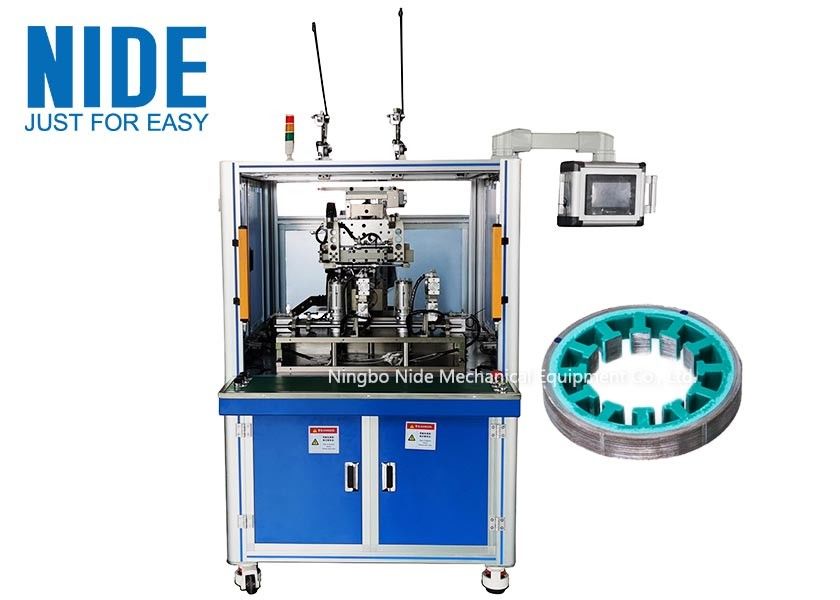
Troubleshooting and monitoring these elements before diving straight into repair can go a long way in reducing costs, labor needs, and downtime, while also providing better security against future failure, since you’ll be better equipped with the necessary information to plan efficient maintenance and upkeep. Sometimes the motor itself has developed a fault - a burnt wire, a broken or bad connection, a winding failure, or a deterioration in critical insulation or bearings. Sometimes the load is jammed, binding, or mismatched. Sometimes motor trouble originates from the power supply, branch circuit conductors, or motor controller. So when a motor fails to start, runs intermittently, produces large amounts of heat, routinely trips its safeties, or operates unreliably, it’s key to isolate the underlying cause of the problem by evaluating basic system levels and conditions. Various elements, including alignment, ventilation, vibration, and lubrication levels, can impact the health of your electric motor.
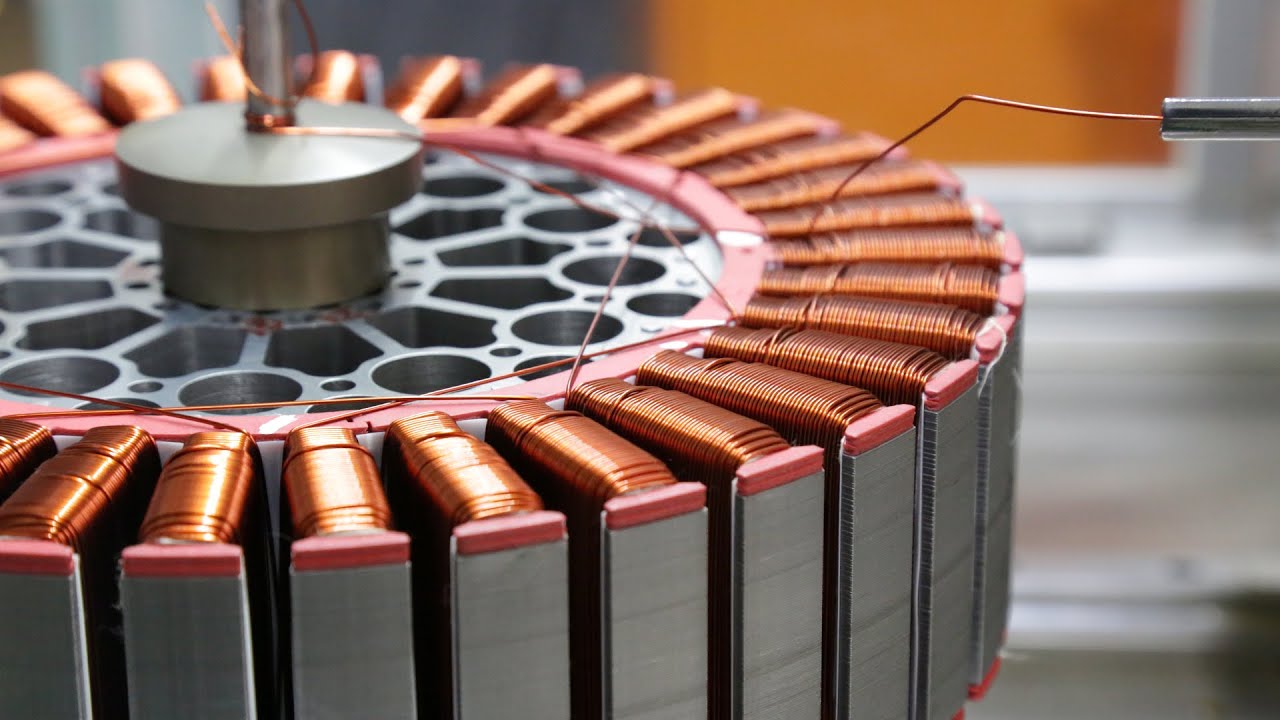
Even basic diagnostic testing can allow for major cost and time savings, reducing the need for maintenance, repairs, and overall labor needs. To keep these variables in check, regular motor testing and monitoring are critical. To have an efficient electric motor running means more than just adequate performance energy efficiency, operating cost, life span, and system reliability are all interconnected with overall motor health.
